Electrical cables are essential components in our everyday lives, powering everything from our homes to our electronic devices. But have you ever wondered how these cables are made? The process of making an electrical cable is fascinating and involves several steps to ensure the cables are safe, durable, and efficient. In this article, we will take a detailed look at how an electrical cable is made, breaking down each step into easy-to-understand sections.
Understanding Electrical Cables
What is an Electrical Cable?
An electrical cable is a type of wire that is used to carry electrical current from one point to another. It is made up of one or more conductors, which are usually made of copper or aluminum, and is insulated with materials like plastic or rubber to prevent electrical shocks and short circuits.
Note:-For high-quality electrical cables, contact Electrical Cable Supplier and Al Arz Electrical Ware Trading. They provide reliable products to meet all your electrical needs.
Types of Electrical Cables
There are various types of electrical cables, each designed for specific uses. Some common types include:
- Power Cables: Used to transmit high voltage electricity from power plants to homes and businesses.
- Control Cables: Used in automation systems to transmit signals and control machinery.
- Data Cables: Used to transmit data signals in computer networks and telecommunications.
The Manufacturing Process
Step 1: Drawing the Conductors
The first step in making an electrical cable is to create the conductors. Conductors are the metal wires that carry electricity. Here’s how they are made:
Selecting the Metal
Most electrical cables use copper or aluminum because these metals conduct electricity well. Copper is often preferred for its excellent conductivity and durability, while aluminum is lighter and less expensive.
Drawing the Wire
The selected metal is drawn into thin wires through a process called wire drawing. This involves pulling the metal through a series of dies, which are small holes that gradually decrease in size. This process makes the metal thinner and longer without breaking it.
Step 2: Annealing the Wire
After the wire is drawn, it is usually annealed. Annealing is a heat treatment process that softens the metal, making it more flexible and easier to work with. The wire is heated to a specific temperature and then allowed to cool slowly.
Step 3: Stranding the Conductors
For many types of cables, multiple thin wires are twisted together to form a single, thicker conductor. This process is called stranding and it provides greater flexibility and strength compared to a single solid wire.
Types of Stranding
- Bunched Stranding: The individual wires are twisted together without any particular pattern.
- Concentric Stranding: The wires are twisted together in a specific pattern, with each layer of wires being twisted in the opposite direction of the previous layer.
Step 4: Insulating the Conductors
The conductors are then insulated to prevent electrical shocks and short circuits. Insulation involves covering the conductors with a non-conductive material such as plastic or rubber.
Types of Insulation Materials
- PVC (Polyvinyl Chloride): A common and inexpensive insulating material.
- PE (Polyethylene): Offers excellent insulation properties and is used in high-frequency applications.
- XLPE (Cross-Linked Polyethylene): Provides high-temperature resistance and is used in power cables.
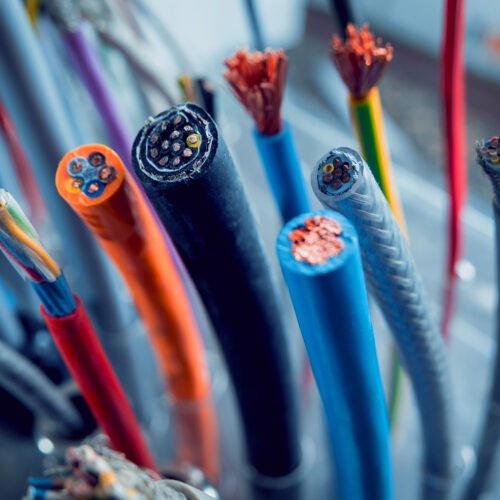
Step 5: Laying Up the Cables
If the cable consists of more than one conductor, the individual insulated wires are twisted together in a process called laying up. This step ensures that the conductors are arranged correctly and stay in place within the cable.
Step 6: Applying the Inner Sheath
The next step is to apply an inner sheath, also known as bedding, around the twisted conductors. The inner sheath provides a protective layer and helps hold the conductors together. It is usually made of plastic or rubber.
Step 7: Armoring the Cable
For cables that need extra protection, especially those used underground or in harsh environments, an additional layer called armoring is added. This layer is typically made of metal, such as steel or aluminum, and protects the cable from physical damage.
Types of Armoring
- Steel Wire Armoring (SWA): Used for cables that need high mechanical protection.
- Aluminum Wire Armoring (AWA): Used for cables that need to be lightweight and resistant to corrosion.
Step 8: Applying the Outer Sheath
The final step in the manufacturing process is to apply the outer sheath. The outer sheath is the external layer of the cable and provides additional protection against environmental factors such as moisture, chemicals, and physical damage. It is typically made of durable materials like PVC or PE.
Quality Control and Testing
Before the cables are ready for use, they undergo rigorous quality control and testing to ensure they meet safety and performance standards. Some common tests include:
- Electrical Tests: To check the conductivity and insulation resistance of the cables.
- Mechanical Tests: To ensure the cables can withstand physical stress and strain.
- Environmental Tests: To verify the cables’ resistance to moisture, chemicals, and extreme temperatures.
Packaging and Distribution
Once the cables pass all quality control tests, they are packaged for distribution. Cables are typically wound onto reels or drums to make them easy to transport and handle. They are then shipped to distributors, retailers, or directly to customers.
Conclusion
The process of making an electrical cable is complex and involves multiple steps to ensure the final product is safe, reliable, and efficient. From selecting the right materials and drawing the conductors to insulating, armoring, and applying the outer sheath, each step is crucial in creating high-quality electrical cables. By understanding how electrical cables are made, we can better appreciate the technology and craftsmanship that goes into these essential components of modern life.
Note :- To Read More Articles Visit on getmeta.